Сжигание предварительно не подготовленных отходов
Метод слоевого сжигания неподготовленных отходов в мусоросжигательных установках наиболее распространен и изучен. В этом случае помимо выполнения санитарно-гигиенических мероприятий можно получить тепловую или электрическую энергию, сократить до минимума расстояние между местом сбора отходов и мусоросжигательным заводом (МСЗ), значительно экономить земельные площади.
Однако при сжигании отходов выделяются твердые и газообразные отравляющие вещества, поэтому все современные МСЗ должны быть оборудованы высокоэффективными газоочистными устройствами, стоимость которых достигает 50% общих капиталовложений на строительство МСЗ.
В Украине построено три МСЗ: в Харькове, Киеве, Севастополе.
На МСЗ сжигают доставляемый на него мусор, без какой бы то ни было предварительной подготовки или обработки.
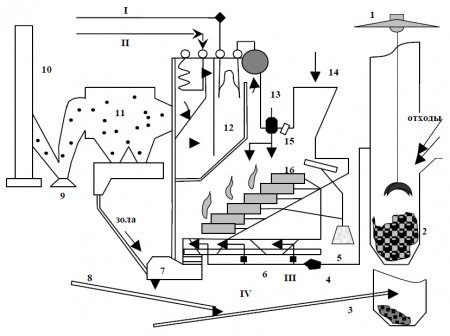
Технологическая схема переработки отходов на мусоросжигательных заводах: 1 – мостовой грейферный кран; 2 и 3 – мусорный и шлаковый отсеки бункера-накопителя; 4 – вентилятор первичного дутьевого воздуха; 5 – станция гидропривода; 6 – паровые калориферы-воздухоподогреватели; 7 – шлакоизвлекатель; 8 – ленточные транспортеры для удаления шлака и золы; 9 – дымосос; 10 – дымовая труба; 11 – электростатический фильтр; 12 – котел-утилизатор; 13 – вентилятор вторичного воздуха; 14 – загрузочный бункер; 15 – растопочная горелка; 16 – колосниковая решетка; I –- пар; II – вода; III – воздух; IV – шлак
При поступлении на завод мусоровозы взвешивают на платформенных автоматических весах. Затем по эстакаде мусоровозы поступают для разгрузки в приемное помещение, оборудованное в виде холла с воротами.
Несколько пунктов разгрузки предусматривают гравитационную выгрузку одновременно нескольких мусоровозов в бункер-накопитель. Мусор из бункера-накопителя частями забирает мостовой кран, оборудованный грейферным ковшом типа «Полип» вместимостью 5 м3 с гидроэлектрической системой управления.
В приемном отделении поддерживается некоторое разрежение воздуха за счет забора из него дутьевого воздуха для поддержания процесса горения ТБО в котлоагрегатах, что предотвращает выброс неприятных запахов и пыли за пределы отделения. Мусор из приемного бункера подают в загрузочный желоб питателя печи котлоагрегата до определенной высоты. Емкость желоба образует буферный резерв питания печи. Образуемая таким образом колонна мусора обеспечивает герметичность между камерой сжигания и загрузочным бункером. Нижняя часть желоба защищена водяной рубашкой от перегрева в случае подъема пламени. Питатель распределяет мусор по колосниковой решетке, на которой сжигают мусор. Она является основным элементом печи.
Имеется несколько видов колосниковых решеток. Наибольшее применение получило топочное устройство, оборудованное обратно переталкивающей колосниковой решеткой системы «МАРТИН» (Германия), шириной 3 м и наклоненной под углом 26° к горизонтальной плоскости. По ширине решетка имеет одну или несколько секций, каждая из которых состоит из 13 рядов чередующихся подвижных и неподвижных колосников. Схема устройства колосниковой решетки и распределение зон горения мусора на ней показаны на рисунке ниже.
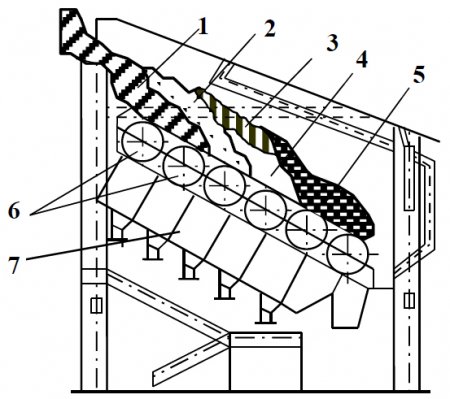
Схема процесса горения в топке мусоросжигательного котла:1 – исходный мусор; 2, 3, 4, 5 – соответственно зоны выхода продуктов, газификации, горения кокса и образования шлака; 6 – колосниковые валки; 7 – подрешеточный бункер для сбора золы и просоров
Каждый второй колосник приводится в возвратно-поступательное движение общим устройством управления. Амплитуда возвратно-поступательного движения в направлении решетки снизу вверх составляет около 400 мм, а число циклов может плавно изменяться от 0 до 60 в час.
Перемещение колосников решетки существенно влияет на процесс сжигания слоя мусора, который при каждом цикле медленно перемешивается и раскладывается по поверхности. Часть горящей массы перемещается ко входу решетки, давая запал для вновь поступающей массы мусора. Таким образом, уже в начале решетки образуется интенсивное пламя, при котором все стадии сжигания – сушка, возгорание и сжигание – происходят одновременно.
Благодаря наличию сильного пламени в начале решетки газы, выделяющиеся на стадии сушки, смешиваются с очень горячими газами горения и сжигания.
Мусор, сжигаемый на решетке, постепенно перемещается вниз, постоянно перемешиваясь. Сжигание мусора завершается приблизительно на 2/3 длины решетки, а на оставшейся части мусор, превратившийся в шлак, постепенно охлаждается под действием подаваемого в топку воздуха.
Гарантийный срок работы колосниковой решетки – около 30 тыс. ч. Температура в топочном пространстве регулируется автоматически и составляет 800...1000°С, что обеспечивает выгорание твердых и газообразных горючих составляющих отходов.
Для обеспечения требуемого качества сжигания, т. е. для получения хорошо перегоревшего шлака, необходимо удалять его одновременно. Шлак составляет около 25% по массе (4...5 т/ч) от общего количества сжигаемых отходов. Для этого колосниковую решетку оснащают барабаном удаления шлака с регулируемой скоростью вращения, что позволяет сглаживать толщину слоя мусора и шлака на решетке, а также удалять шлак в бункер шлакового экстрактора.
Горячий шлак падает в бункер, а затем в бак с водой, в котором охлаждается до 80...90?С. Из бака шлак удаляется толкателем, который проталкивает его в желоб, установленный с обратным уклоном. Конструкция желоба позволяет, с одной стороны, уплотнять удаляемый материал без риска закупорки рабочего сечения желоба, а с другой – стекать избыточной влаге. Таким образом, потери воды на гашение сводятся к минимуму, т. е. на испарение и поглощение ее шлаком.
Далее охлажденный шлак по системе ленточных транспортеров проходит через виброполотно, с которого из шлака удаляют металлические частицы, для чего над ленточным транспортером устанавливают магнитный сепаратор, оборудованный мощным электромагнитом. Куски металла удаляют в специальные емкости, а освобожденный от металла шлак поступает по ленте в шлаковый отсек бункера-накопителя. Зола из-под воздушного короба и из бункеров котла удаляется вместе со шлаком.
Для обеспечения процесса горения отходов подают воздух, нагнетаемый вентилятором первичного дутья через короб, установленный под решеткой и состоящий из нескольких отсеков или зон. Каждая зона подачи воздуха под решетку обеспечивает впуск определенного количества воздуха под решетку и в слой мусора для обеспечения горения; сбор и удаление мелких частиц, просеивающихся под решетку.
В нижней части в подрешеточной зоне установлены воронки асимметричной формы, которые предназначены для сбора и удаления просева.
Дополнительно воздух подается вентилятором вторичного дутья под высоким давлением через сопла, расположенные на передней и задней стенках камеры горения, для завершения окисления и полного сжигания газов в нижней части камеры сжигания.
Рассмотренная технология слоевого сжигания отходов направлена на санитарно-гигиеническое (огневое) обезвреживание ТБО с получением тепловой энергии, которую утилизируют через котел, установленный над колосниковой решеткой. Возможно различное использование энергии: городское отопление; пар для промышленных установок; выработка электроэнергии для собственных нужд или для сбыта в единую систему.
Выбору технологии обезвреживания и переработки ТБО методом сжигания предшествует детальное технико-экономическое обоснование схемы сбыта получаемой тепловой энергии, так как строительство МСЗ требует больших капиталовложений. Оптимальная схема сбыта вырабатываемой энергии – нужды централизованного теплоснабжения. В этом случае пар, вырабатываемый МСЗ, можно использовать для подогрева сетевой воды в специальном дополнительном подогревателе, установленном после основных подогревателей.
МСЗ проектируют и строят как обособленные предприятия, оснащенные всем необходимым оборудованием (химической водоподготовкой, деаэрационной установкой, необходимыми подогревателями, питательными насосами и т.п.). На МСЗ предусматривают также склады, служебно-бытовые помещения и т. д.
Санитарно-гигиенические требования к чистоте атмосферного воздуха постоянно повышаются. Вместе с тем, как подтверждает практика, установки по сжиганию ТБО могут служить источником загрязнения воздушной среды взвешенными частицами и недожога, а также вредными газообразными примесями. Поэтому при их проектировании особое внимание уделяют совершенствованию средств по снижению выбросов вредных примесей. Физико-химические свойства отходящих газов при сжигании ТБО зависят от морфологического и фракционного составов, теплоты сгорания отходов и т. д. Эти показатели существенно меняются в зависимости от климатических условий района и сезона года. Влажность ТБО колеблется в пределах 52...58% в зависимости от сезона года, а содержание влаги в дымовых газах меняется в пределах 95...119 г/м3.
Существует три вида выбросов из мусоросжигательных установок: газы, выходящие из дымовой трубы; сточные воды; летучая зола и шлак.
Наиболее вредными выбросами мусоросжигательных установок считают отходящие газы и летучую золу. Поскольку основной вредной составляющей дымовых газов являются содержащиеся в них взвешенные частицы и отравляющие вещества, то их концентрацию и принимают в качестве главного показателя санитарно-гигиенического аспекта работы таких сооружений.
Наиболее жесткие нормы, ограничивающие выброс твердых газообразных веществ, введены в Германии – концентрация золы в дымовых газах сжигательных установок не должна превышать 100 мг/м3 (при СО2 – 7%).
Зола, образующаяся при сжигании ТБО, состоит в основном из двух компонентов: минералов и несгоревших частиц органических соединений.
Содержание недожога в процентах определяется конструктивными особенностями топочного устройства, а также технологическими условиями процесса горения. Обычно оно не превышает 2%, а при неблагоприятных условиях может достигнуть 15%. Концентрация золы в дымовых газах мусоросжигательных установок составляет примерно 2...5 г/м3 сухого газа. При увеличении содержания бумаги в отходах, подвергающихся сжиганию, наблюдается более высокая концентрация золы в отходящих газах. Содержание в отходах различных твердых компонентов приводит к резкому снижению концентрации золы (до 0,5 г/м3).
От дисперсного состава золы зависит не только работа газоочистного оборудования, но и выбор средств очистки дымовых газов. Размер частиц золы уноса влияет на скорость осаждения, площадь удельной поверхности, их смачиваемость и т.д. Распределение взвешенных частиц золы уноса в зависимости от размера частиц следующее,%: менее 5 мкм – 9...22; 5...10 мкм – 10...16; 10...20 мкм – 13...15; 20...30 мкм – 6...14; более 30 мкм – 31...54. Значительные колебания процентного содержания частиц в каждой фракции объясняются непостоянством состава ТБО.
При выборе газоочистных устройств следует учитывать, что труднее всего улавливаются частицы размером менее 5 мкм, масса которых может достигать 22...25% общей массы твердых примесей, содержащихся в очищаемых газах.
Выбор газоочистных устройств зависит от объема очищаемых газов, их запыленности, желаемой степени очистки (КПД улавливания), физических параметров газового потока (скорости, температуры, влажности, агрессивности), физико-химических свойств взвешенных частиц (дисперсности, слипаемости и т. д.).
Выбирают и оценивают работу газоочистительного оборудования в первую очередь по степени очистки уходящих газов и только во вторую – по ее стоимости.
Н.В. Нечипорук, В.Н. Кобрин, С.А. Вамболь, Е.А. Полищук, В.Ю. Колосков